Repairing instead of throwing away: How Kärcher appliances get a second life
From product development to the uncomplicated repair process: Kärcher makes repairability a consistent principle. While new EU regulations are setting standards, the company is showing how durable products and innovative business models complement each other.
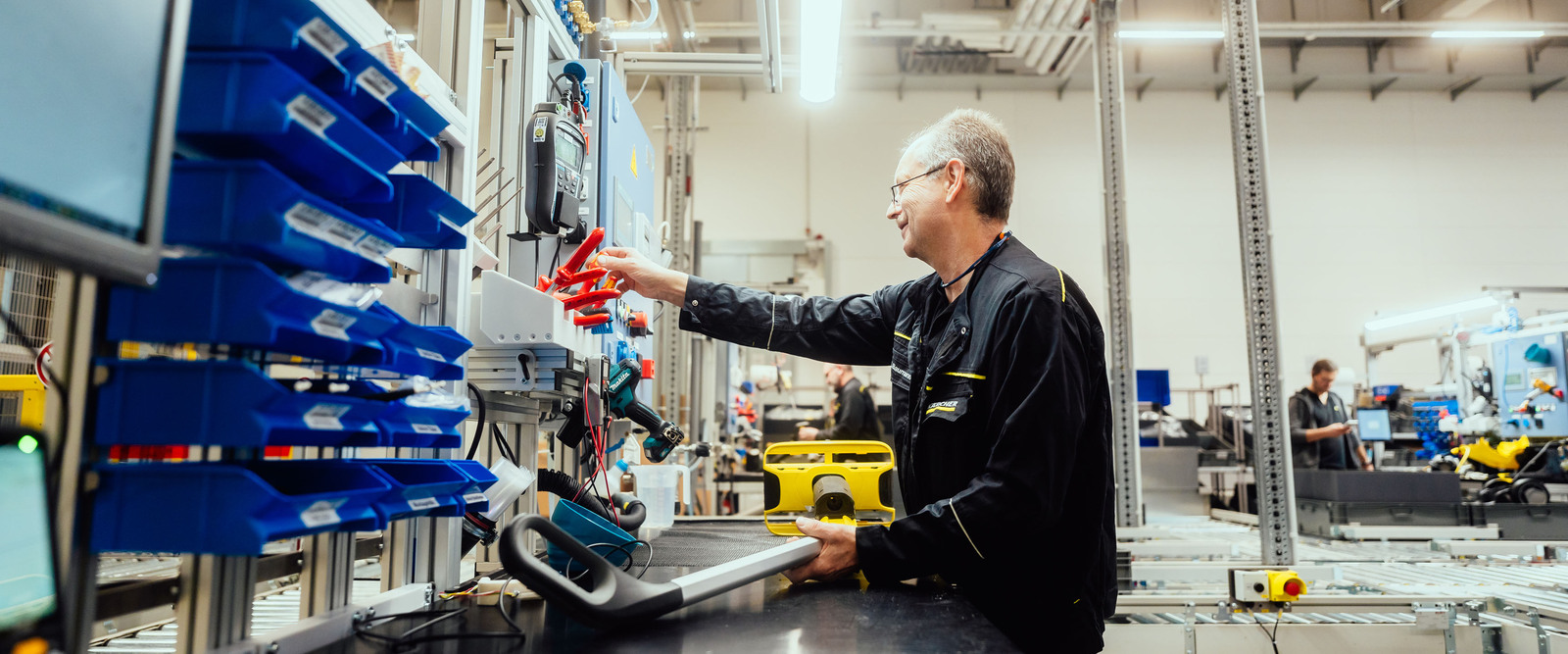
As easy as ordering pizza
“It's as easy as ordering a pizza,” says Sarah Lang, Senior Business Consultant Aftermarket & Services at Kärcher, explaining the digital repair process for Home & Garden appliances. The sophisticated system guides customers through the entire repair process. The journey begins on the Kärcher website: After logging into the “my Kärcher” customer portal, users enter their appliance data and choose from typical fault descriptions. They are given practical tips on how to help themselves - sometimes a supposed defect can be rectified in a few simple steps.
Transparent process
If customers opt for a repair and it is not a warranty case, they are immediately informed of the fixed price. This is based on the type of device, not the type of defect - a transparent solution that eliminates surprises. Customers can then choose between various shipping options: Pick up at home or drop off at a parcel store. The system automatically generates all the necessary shipping documents.
Particularly transparent: customers are always kept informed during the repair. They know when their device has arrived at the service center, when it will be repaired and when it is on its way back. The system is already available in most European countries and in Japan and is to be expanded further.
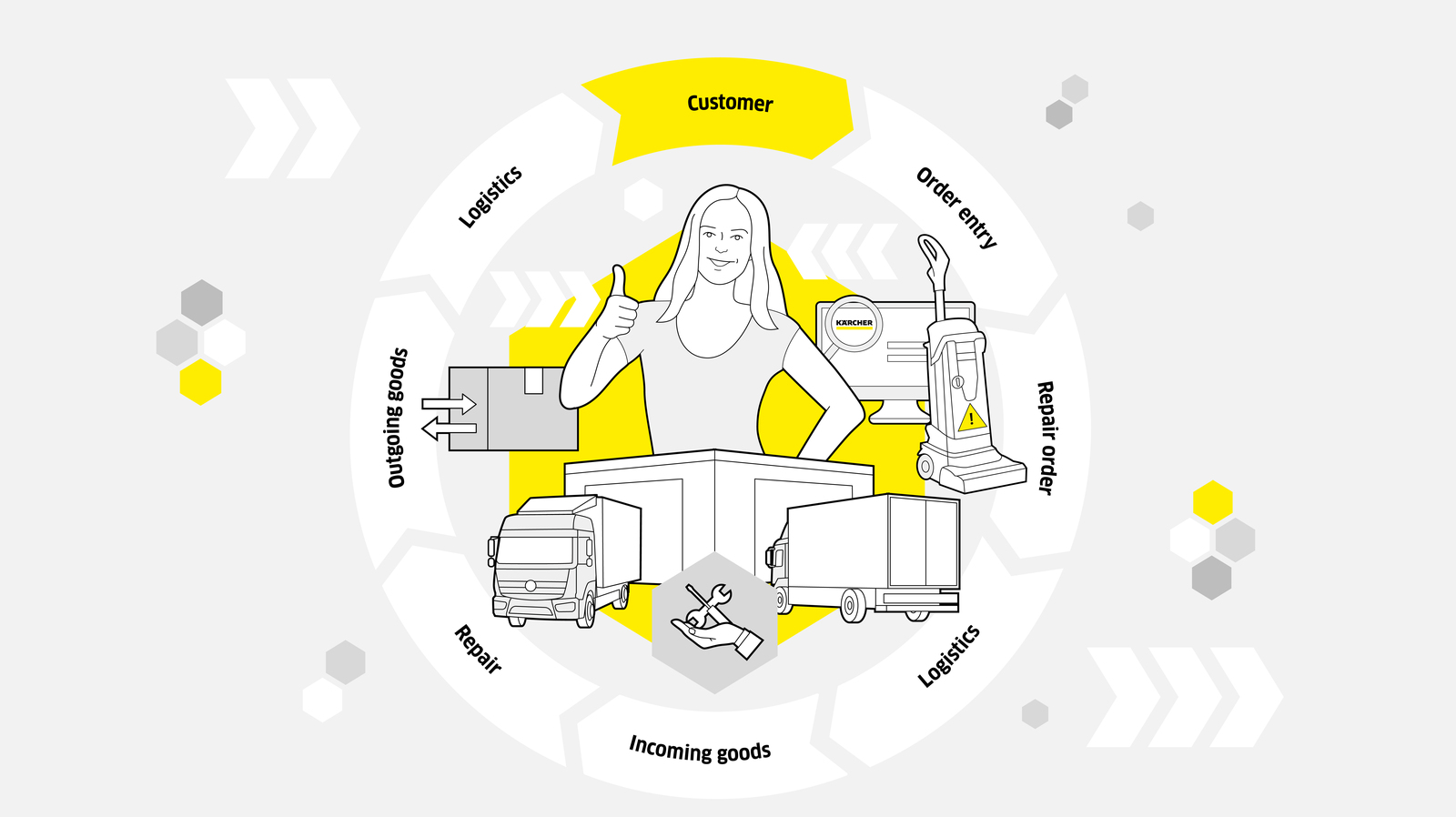
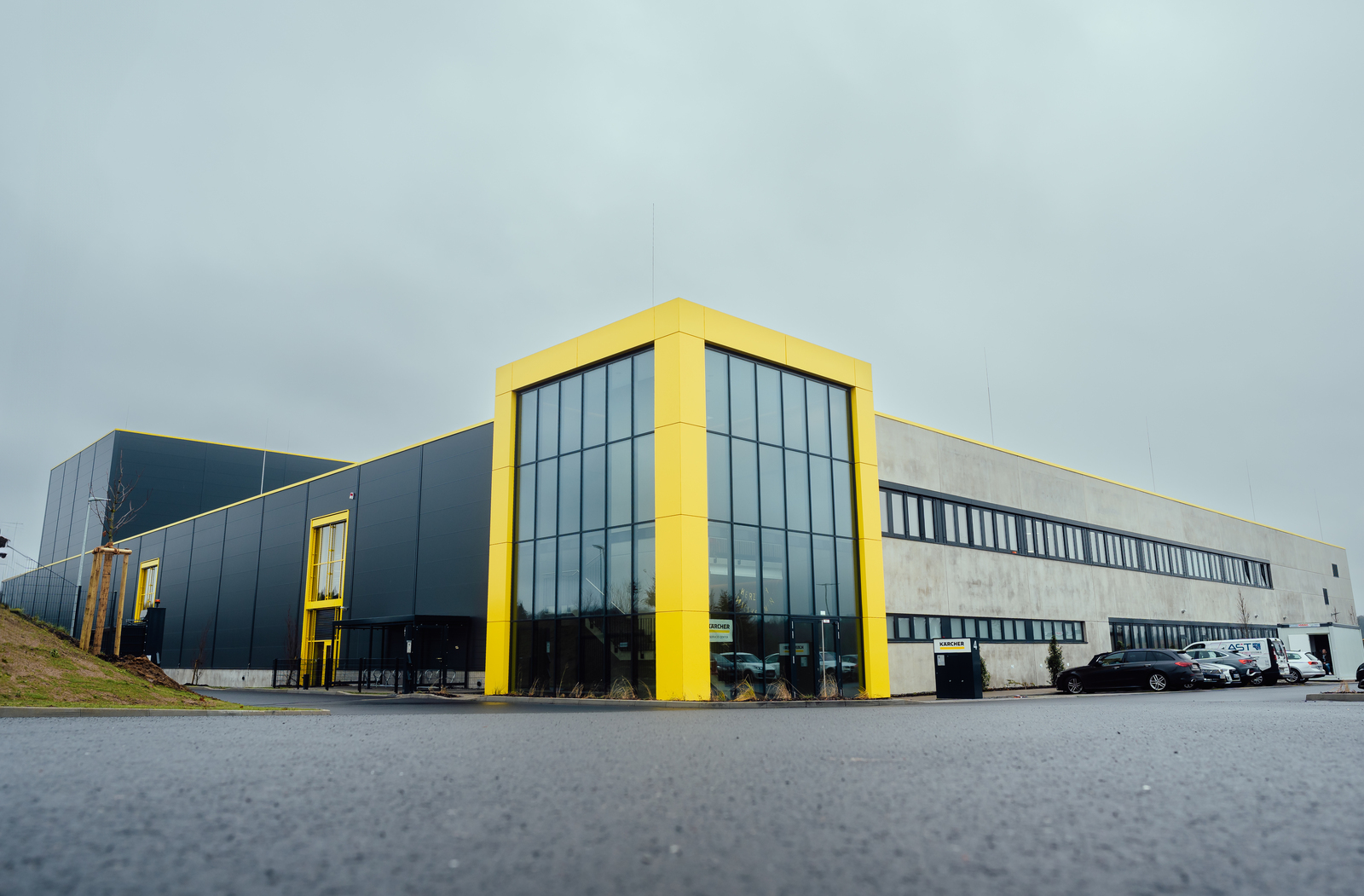
High-tech meets craftsmanship: the Ahorn repair center
An important building block for this process in Europe is the new service center in Ahorn, Baden-Württemberg. The facility, in which around 26 million euros have been invested, sets standards in terms of automation and sustainability. “It is one of the most modern repair plants in Europe, perhaps even in the world,” says Lang.
Once the appliances have been received, they are automatically sent to the specialized technicians. They focus on specific types of appliances - this pools expertise and enables efficient repairs. The center doesn't just handle traditional repairs: returns are also refurbished here and used devices are made fit for a second life. Every year, the service center in Ahorn repairs up to 200,000 appliances from 9 European countries.
The infrastructure is also designed for sustainability: The water used to test pressure washers is treated and used to flush toilets. Packaging is done exclusively with paper materials.
Repairability starts with the design
Whether an appliance can be repaired well is decided long before a defect occurs - namely in the development phase. At Kärcher, service experts accompany the entire product development process. Their input influences the design decisions: Where gluing was previously used, screw connections are increasingly being used today. This makes it easier to open and close housings and assemblies during repairs and allows them to be reused.
Sunay Gündogan, Business Development Manager for Aftermarket & Services, explains: “In order to systematically improve repairability, Kärcher has developed its own internal repair index. This takes into account various factors based on the legally required repair indices, such as the French Repair Index.” The French repair index includes topics such as spare parts prices and availability. Gündogan is proud of the latter: “We offer spare parts availability of over ten years for many of our appliances. With our spare parts webshop, customers can also order spare parts themselves and carry out simple repairs.” In total, Kärcher keeps around 38 million individual spare parts permanently in stock. These are stored in Kärcher's Global Parts Center in Obersontheim, Germany, from which over 3 million individual spare parts are shipped worldwide every year.
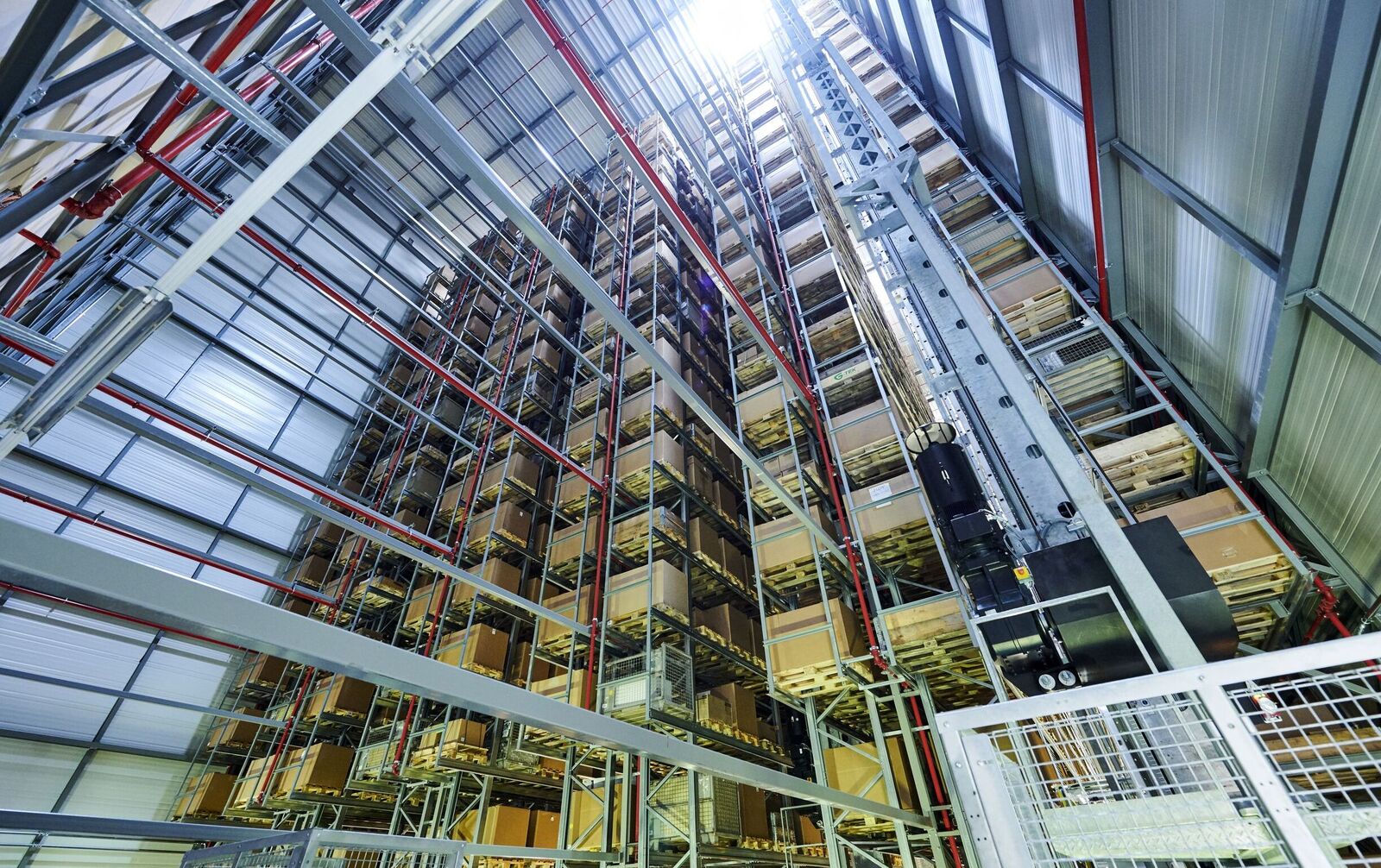
Regulation as an opportunity for innovation
Legislators are pushing the issue of repairability. Repair indices such as those in France make the reparability of appliances transparent for consumers. Belgium is following this example, and new standards are also being prepared at EU level. The “Ecodesign for Sustainable Products Regulation” will define industry-wide requirements in the future.
Kärcher is preparing intensively for these developments. Saskia Schneider, Sustainability Management Products & Customers, explains: “We are continuously analyzing new legislation and its impact on our products.” Kärcher is involved in five industry associations and helps shape the discussion about new standards. This is not just about reparability: more than 20 sustainability aspects are taken into account, from material selection, reparability and service to the circular economy.
The challenge lies in the daily implementation: while the repairability of the products themselves is already at a good level, Kärcher is working on the global implementation of the repair processes. The service center in Ahorn is a role model that shows what modern repair services can look like. “Repairability is the basis for everything else,” emphasizes Schneider. “Only products that can be repaired well can be used for a long time, successfully reconditioned and integrated into recycling systems.”
Professional Service: Different requirements, same principles
There are different rules for Professional devices. Unlike in the Home & Garden sector, technicians come to the device — if only because Professional machines are much larger. A worldwide network of over 1,300 Kärcher technicians and 4,000 service partners is therefore available for repairs. The technicians are trained for professional devices and identify many problems in advance thanks to digital tools such as visual remote diagnostics. If a longer repair is necessary, they provide replacement equipment so that customers can continue working.
Sunay Gündogan explains: “With a strong focus on the circular economy and the repairability of machines, our vision is to extend the life of our products as much as possible. By encouraging our customers to delay the purchase of new machines with our service packages, we are actively helping to reduce overall CO2 emissions and the use of raw materials.” The inclusion of regular maintenance work in the Kärcher service packages not only significantly reduces the likelihood of unexpected failures, but also extends the life of the machines.
Sustainable aftermarket business models are also offered as an alternative to buying a new product. For example, Kärcher is working on expanding its range of used machines. To do this, the company buys back used Professional machines, professionally refurbishes them and brings them back to market. In addition, Kärcher already offers equipment for rent in over 25 countries, with this offering being continuously expanded to other countries.
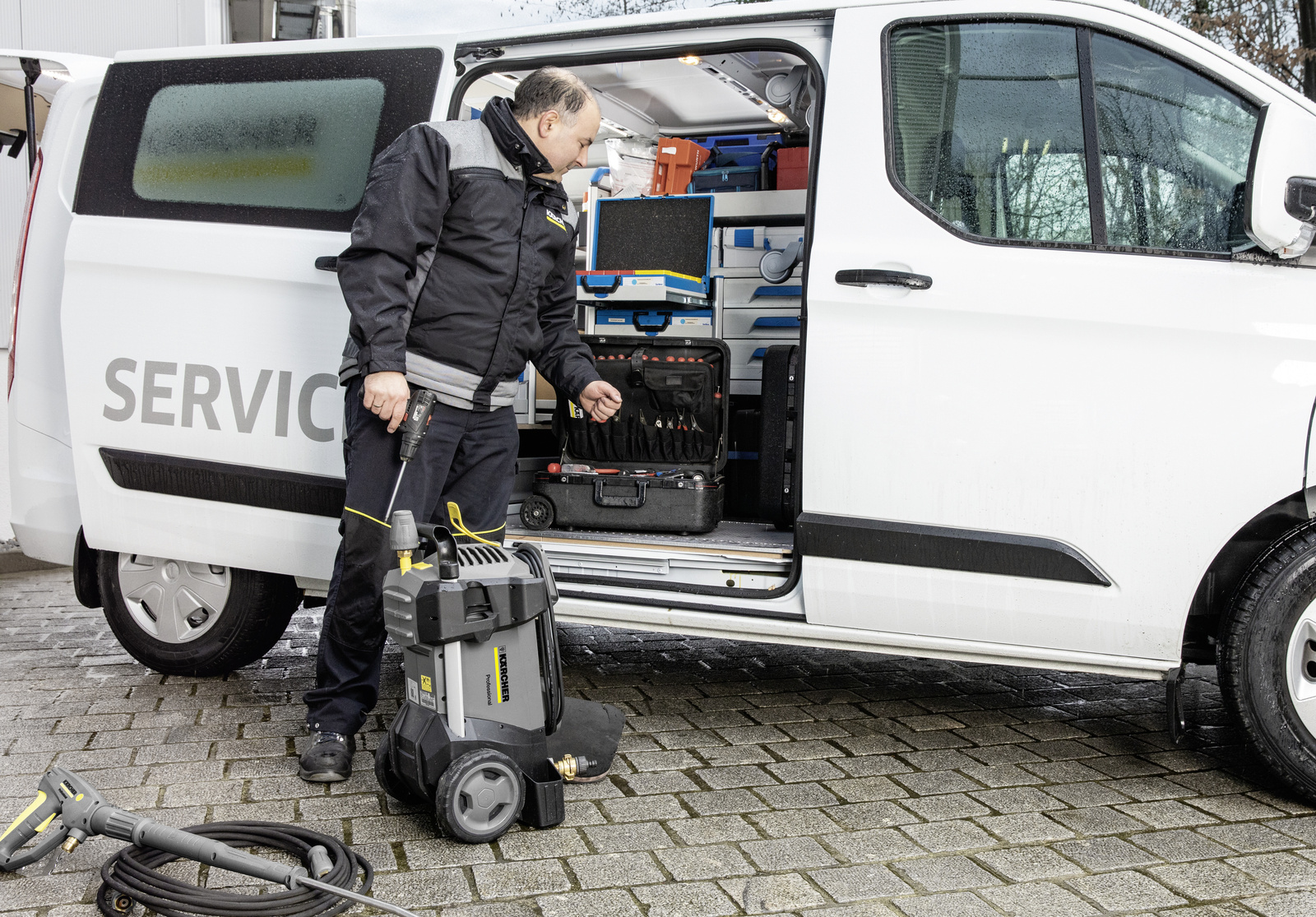