Cleaning and maintaining natural stone
Natural stones with the same or similar look can have very different technical properties, particularly with regard to sensitivity to alkalis or acids, firmness and water absorption. It is these factors which determine which stone is suitable for which purpose and how it must be maintained in order to retain its appearance for a long time. Before cleaning, you must therefore have thorough knowledge of the stone's properties based on its mineral composition and surface treatment, as well as its usage.
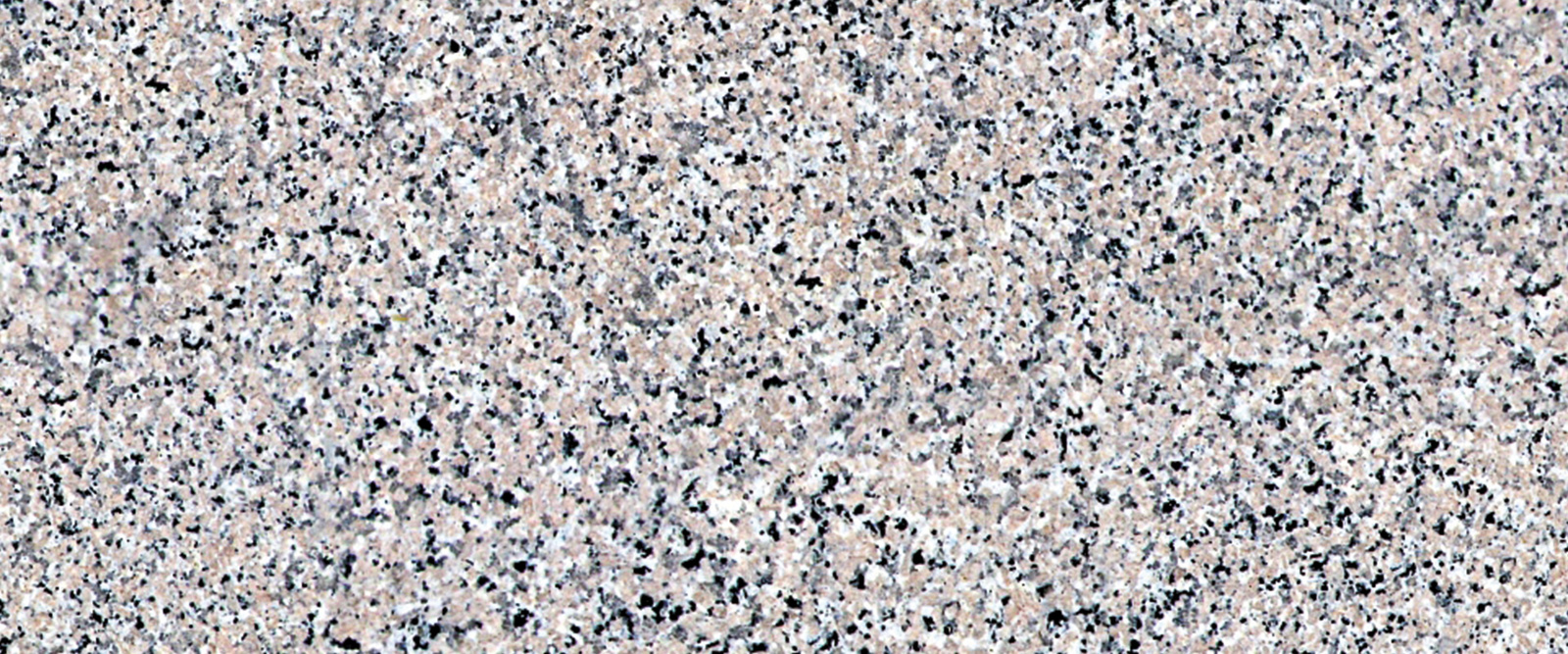
Knowing natural stone properties
Natural stones are used in many different areas, including in industry, in horticulture, on façades, in art, as masonry or in interior finishing, where they are often used as floor coverings. They are first mined in quarries and sawn to size in stone-processing operations. Their surfaces are then treated using a machining method – whether polishing, flaming, grinding or sanding. No artificial material has such versatility in colours and surface finishes. Natural stones with the same or similar look can have very different technical properties, particularly with regard to sensitivity to alkalis or acids, firmness and water absorption. It is these factors which determine which stone is suitable for which purpose and how it must be maintained in order to retain its appearance for a long time.
Natural stones can be classified into hardness levels based on technical processing criteria: Hard rock (gneiss, granite, quartzite, basalt and gabbro), medium-hard rock (marble, Solnhofen limestone, Jurassic stone and serpentine) and soft rock (lime-bound sandstone, trass and slate). This classification helps to estimate the mechanical strain on the stones. This is not only relevant for processing them but also for cleaning them. For instance, all hard rocks have similar chemical properties – they are usually scratch- and alkali-resistant. This is why they are often used in outside areas where they are placed under high strain. In contrast, soft rocks are more delicate and you must therefore avoid cleaning them with hard brushes, which could quickly cause scratches.
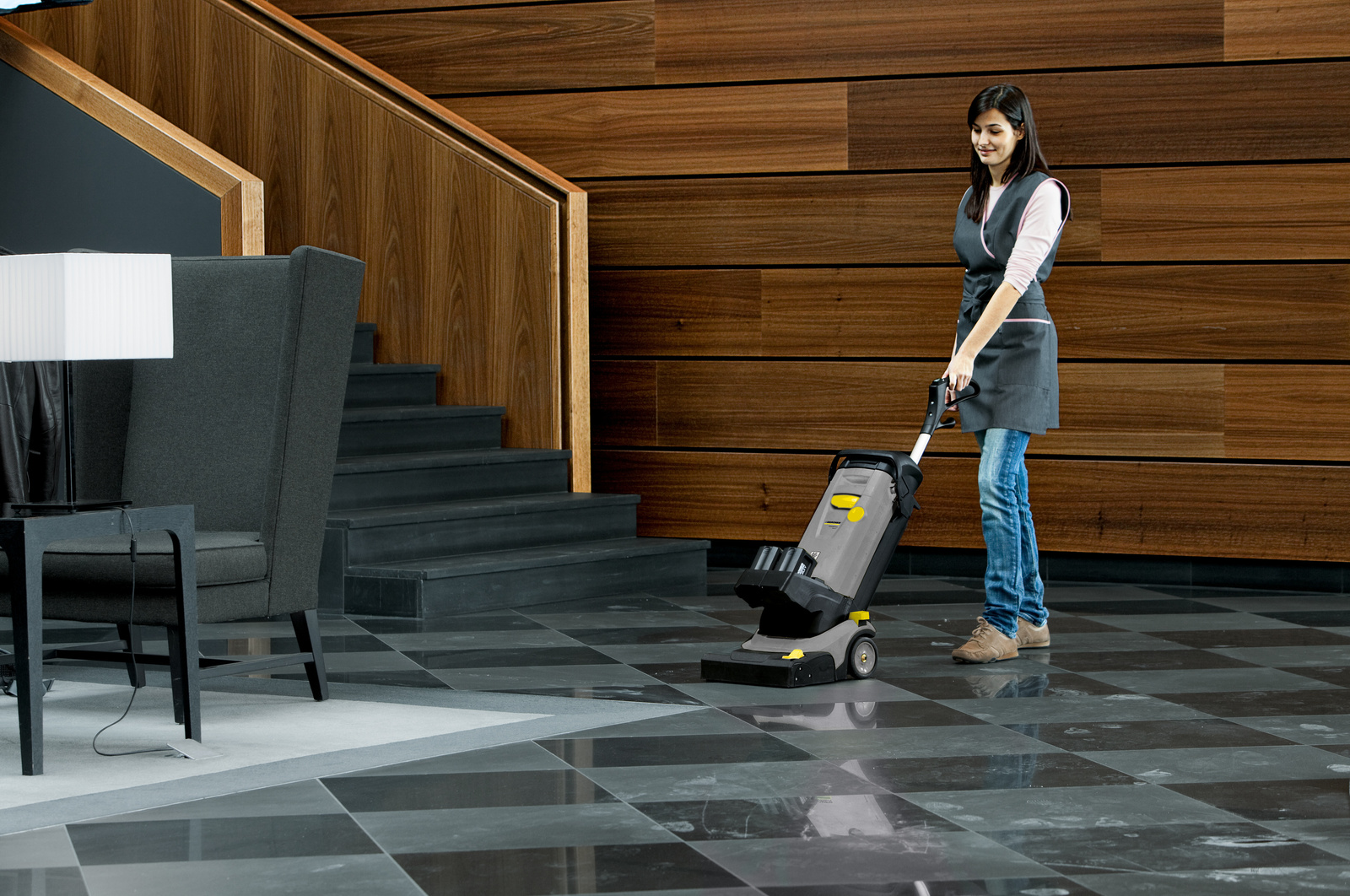
The way in which a stone is processed also has an impact on the cleaning requirements. Polished floor coverings made of medium-hard stone can become matt if alkaline cleaning agents with a pH value of over 12 are used with excessively hard brushes/pads.
Correctly cleaning and maintaining natural stone floor coverings is essential if the stone is to keep its characteristic look over many years. Before cleaning, you must therefore have thorough knowledge of the stone's properties based on its mineral composition and surface treatment, as well as its usage. The wear and dirt on the stone is closely connected to these factors.
Knowing the fundamentals – such as the type of stone and its properties – means that cleaning and maintenance errors can be avoided, as well as their unwelcome consequences (including dullness, stains and colour deviations).
Preventing damage to floor coverings
Natural stones with a low level of hardness, such as marble, are relatively easy to scratch. To protect the flooring in reception halls, for example, it make sense to install a system for catching dirt upstream in order to keep penetration by coarse dirt, such as sand and small stones, as low as possible. This zone should be sufficiently large and should measure between six and eight strides. When it comes to regular cleaning, it is also sensible to start in the area in front of the building because the majority of dirt in buildings is brought in on foot.
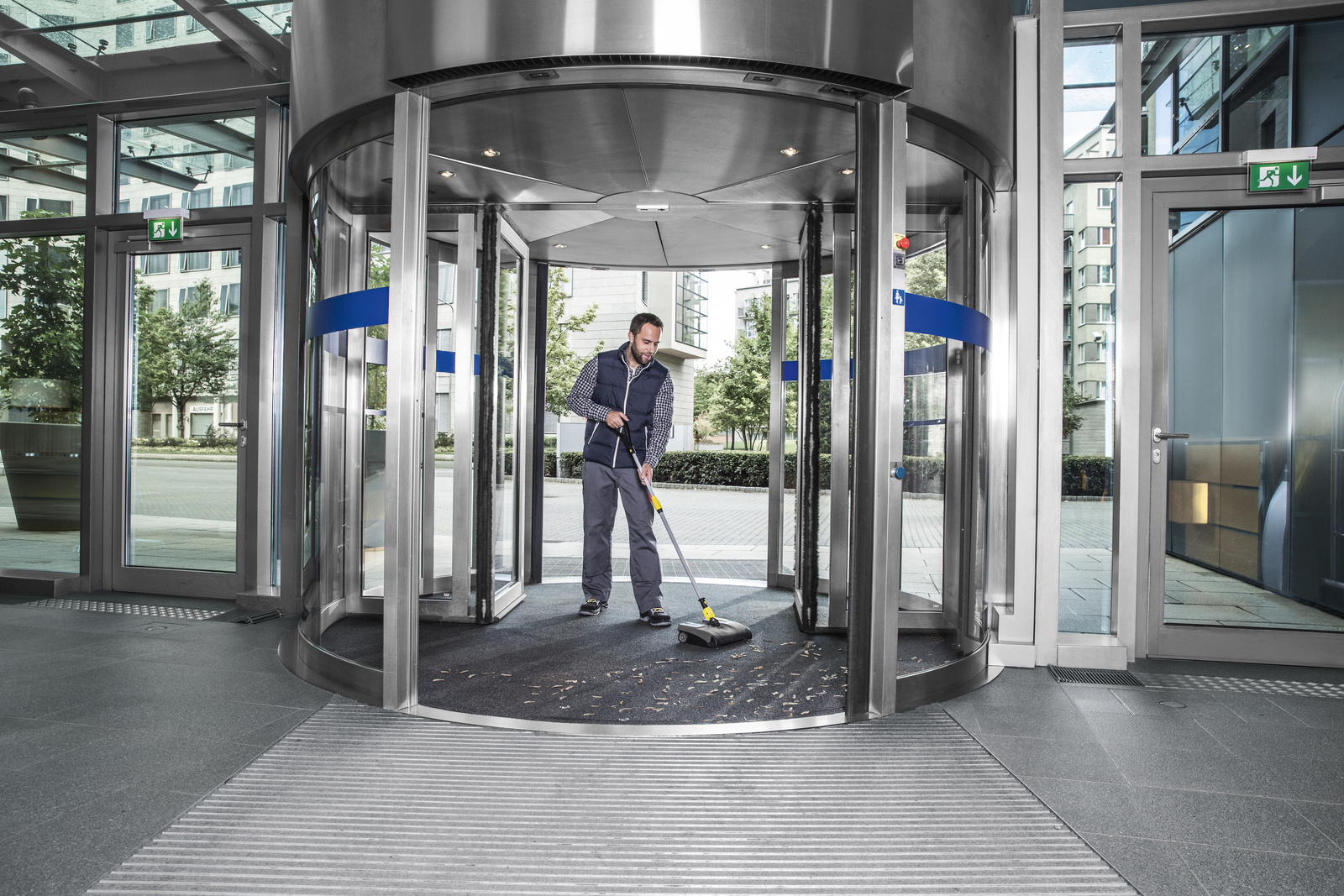
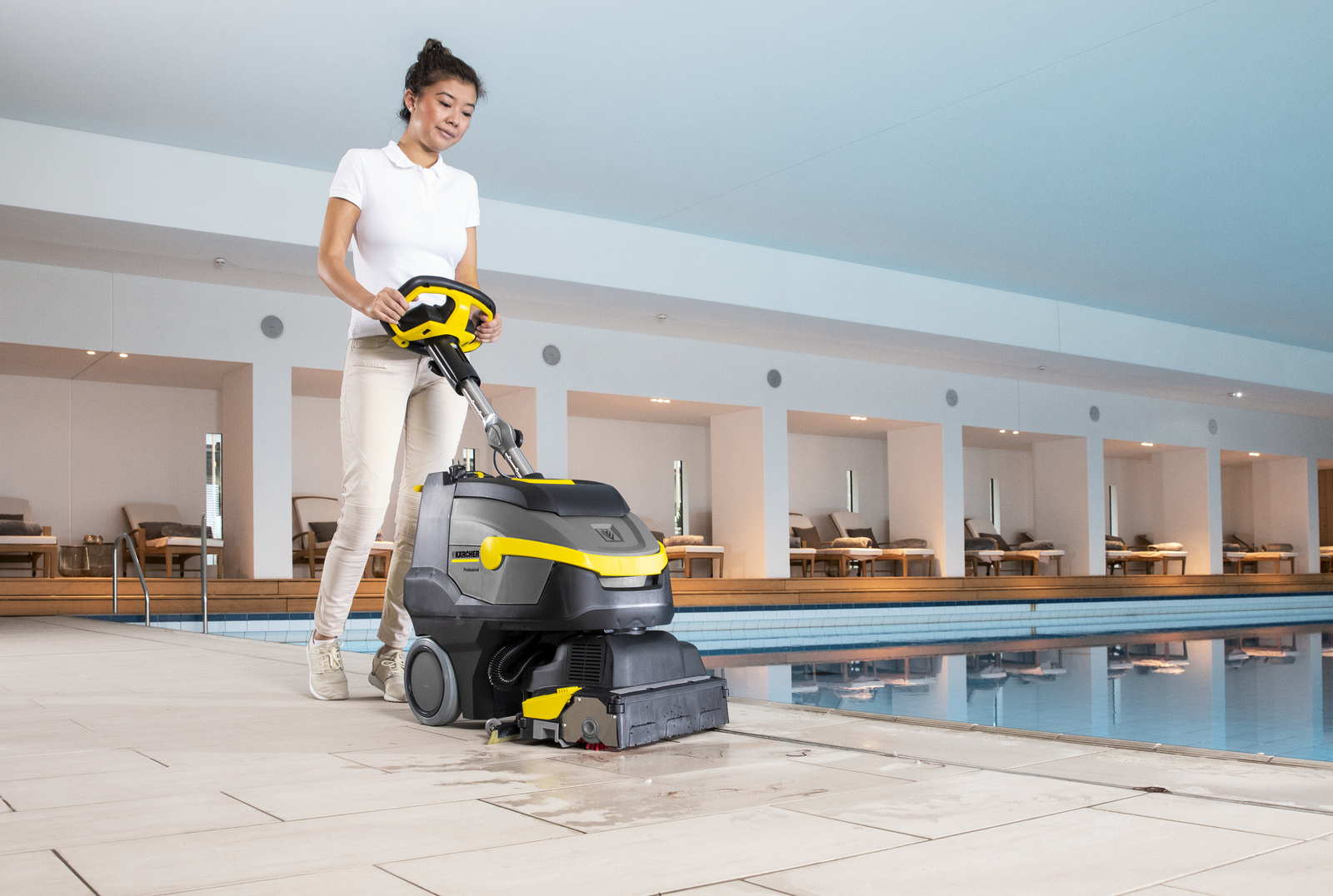
Should natural stone be cleaned manually or mechanically?
Depending on the size of the floor covering to be cleaned and how full of objects and furniture it is, it will be more cost-effective to use a professional scrubber drier than manual cleaning methods starting from an area of around 100 square metres. This is because machines can clean larger areas in a shorter space of time, thus increasing productivity. Not to mention the fact that having different tanks for fresh and dirty water reduces the risk of cross-contamination and users do not come into contact with the dirty water. Moreover, operators are put under less physical strain. Thanks to the precisely adjustable brush contact pressure, the mechanism can be adapted to cleaning requirements with great precision. The suction function ensures that the dirty water is sucked up again and that the floor dries and can be walked on again immediately after cleaning. The scrubber drier with roller technology is a particularly well-suited solution for hewn/textured natural stone floor coverings because the roller brushes are excellent at penetrating the floor covering's surface texture and joints in order to loosen the dirt. In this case, the wiping device's inability to glide on textured flooring when wet wiping, and the subsequent quick wear of the cleaning textiles, has a detrimental effect.
It may be worth using manual cleaning equipment – such as a large surface wiping machine – for small areas, those filled with objects and furniture, and hard-to-reach areas. Moreover, manual cleaning has the upper hand when it comes to cleaning right up to the edge.
Maintenance cleaning of natural stone floor coverings
Maintenance cleaning is a repetitive cleaning task to be performed at set time intervals, such as on a weekly basis.
There is always the option of wiping and collecting dust, particularly on polished natural stone floors, and this cleaning method is suited to coarse dust removal. However, generally speaking, wet cleaning is predominantly used for natural stone floors.
When performing maintenance cleaning on natural stone floor coverings, you can maintain their original appearance by using appropriate wipe care products or floor shine cleaners. It is important to avoid applying an excessive dose because the traces of wiping may become visible, particularly on sanded or polished floors. This also results in the formation of bodies of cleaning agents, which give floor coverings a matt finish. Since the stones may contain metal oxides due to their formation process, there is the risk of rust generation with excessive wet wiping or if water is on the surface for too long.
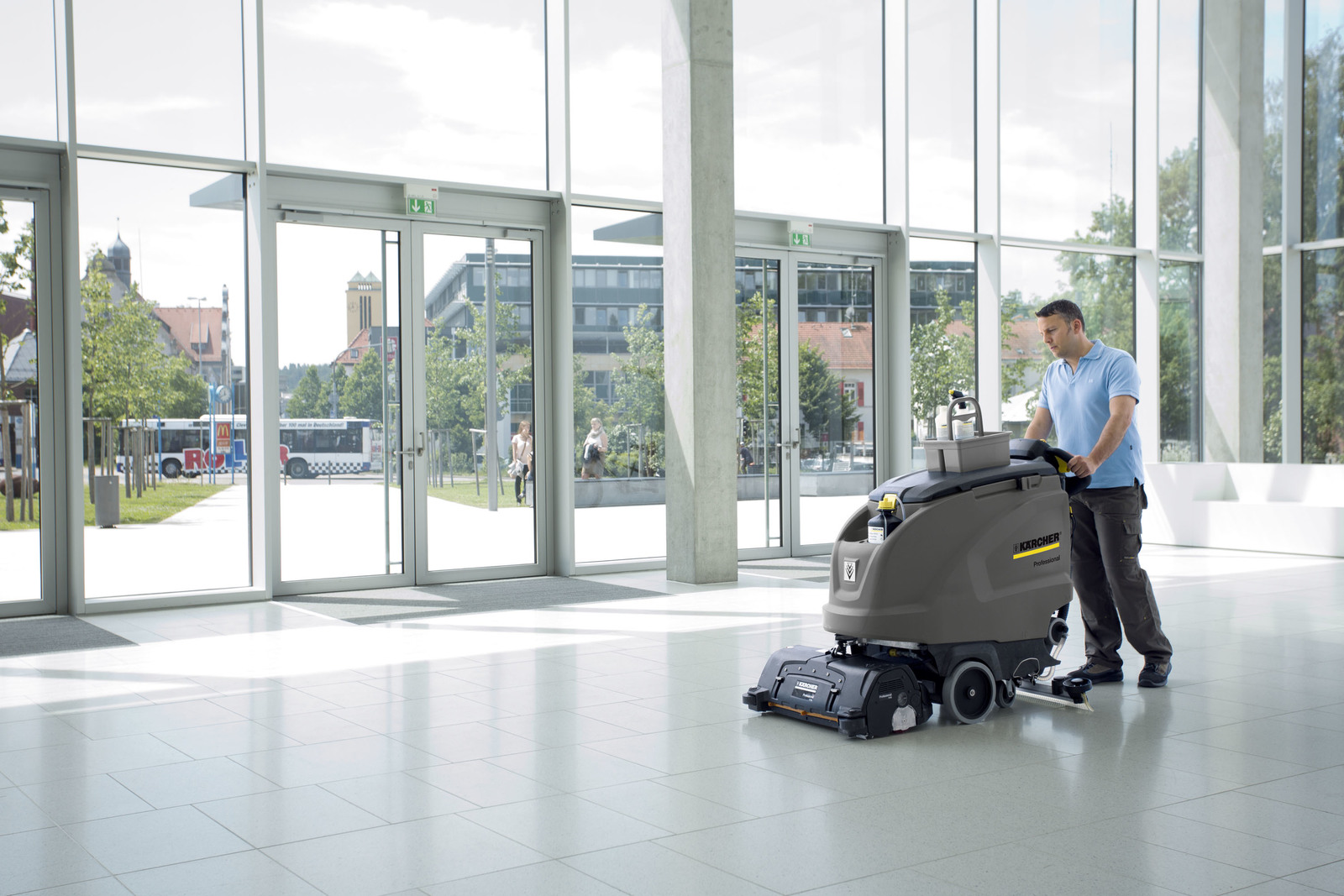
Deep cleaning/intensive cleaning of natural stone
During deep cleaning, stubborn dirt and/or worn protective coatings or other residues which may detract from the look of a surface are removed. Deep cleaning is generally only carried out in longer time intervals.
If a natural stone floor is being relaid, deep cleaning is first required in order to remove any stubborn dirt generated during construction work.
The first step is to remove the loose coarse dirt by sweeping or vacuuming it. Stubborn contaminants, such as varnishes and paints, are removed using a wooden spatula or blade. Dispersion paints can be effortlessly removed using an alkaline deep cleaner. Apply the alkaline deep cleaner in an undiluted form, leave it to soak for approximately five minutes and scrub it with a green hand pad. In the case of slate, which is alkali-sensitive, you should only use the mechanical method with a wooden spatula or blade. Gypsum and mortar residues can be removed using a spatula. Since mortar contains silica sand, you must be particularly careful to cause no scratches on highly polished areas.

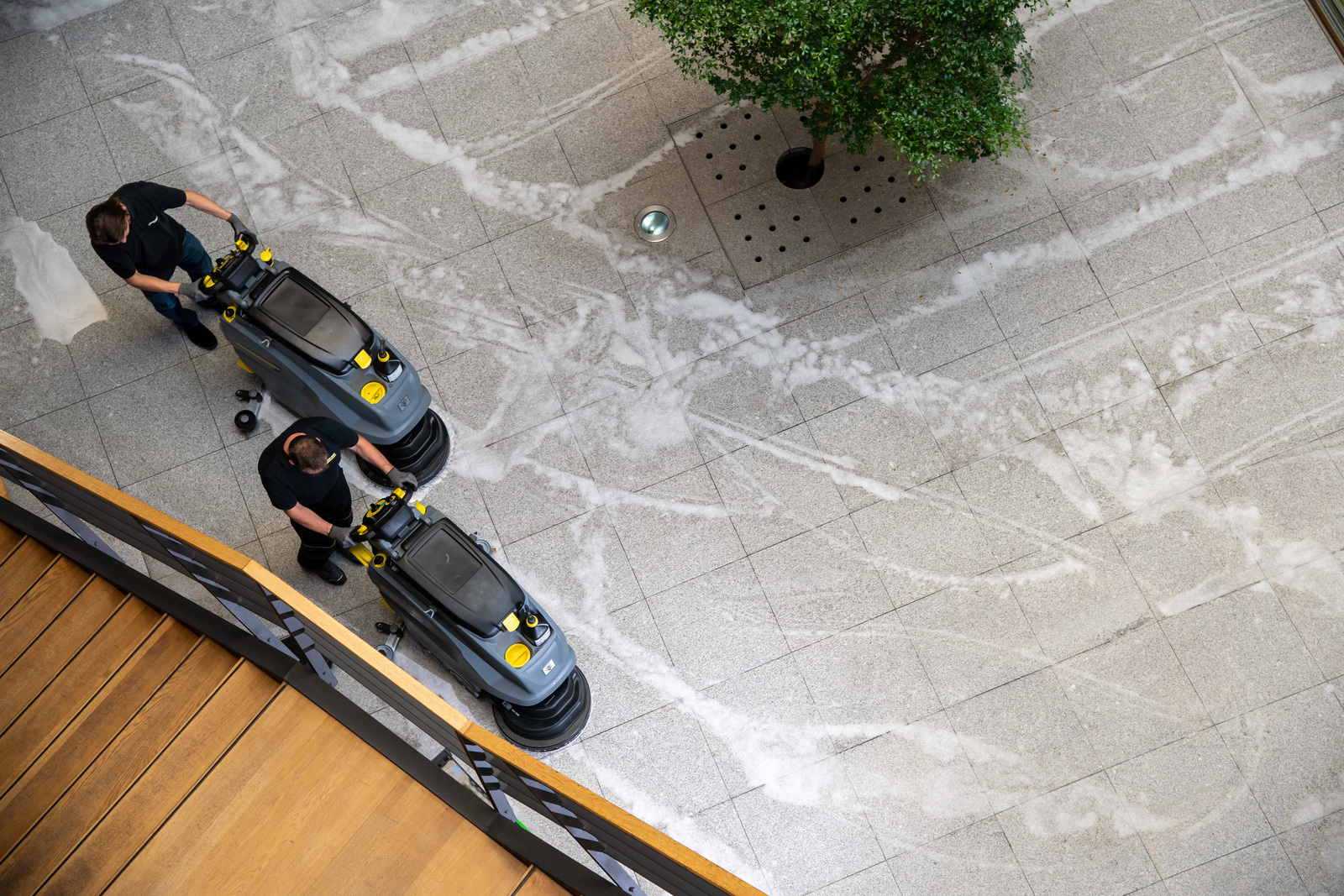
Cement film removal
Grouting a natural stone floor covering generally leaves behind a cement film. This film can be removed after thoroughly pre-rinsing the floor covering with an acidic cleaner. You should test the reaction of the floor covering (any changes in colour hue) to the acidic cleaner on an inconspicuous area beforehand. Before starting the actual cleaning process, the area to be cleaned should also be pre-wetted with clean water such that the joints are saturated with moisture and not damaged by the acidic cleaner (pH value 0.7).
Particular care must be taken on floor coverings which are acid-sensitive, such as marble, Jurassic stone, Solnhofen limestone and travertine. For acidic deep cleaning, it is therefore recommended that you use a scrubber drier with roller technology in a one-step method. The cleaning fleet is applied to the floor, the surface is scrubbed and the dirty water is sucked away immediately in the same step. This ensures that the acidic cleaning solution is only in contact with the natural stone for a few seconds and does not cause chemical burns. This process is not possible with a single-disc machine because it does not have a suction function and the acidic cleaner would be left on the surface for too long before being sucked up again by a wet and dry vacuum cleaner.
The cement film is effortlessly removed thanks to the high-quality mechanics of the roller technology (contact pressure: 210 g/cm², 1100 rpm), which take effect on the floor without any negative consequences. In the case of particularly stubborn dirt, this process should be repeated multiple times. For smooth/polished areas, it is recommended that you use green roller pads (high hardness). Meanwhile, for hewn/textured surfaces, it is recommended that you clean with the red standard brushes or the orange brushes with different bristle heights.
For an acid-resistant floor covering, such as granite, it is possible to use a two-step method. This means that the acidic cleaning solution is initially applied to the floor without a suction system. During a contact time of approximately five minutes, the scrubber drier with roller technology is guided from side to side across the surface multiple times, scrubbing the floor in the process. The second step is to suck up the dirty water. The floor covering is then rinsed with clean water until it has been neutralised.
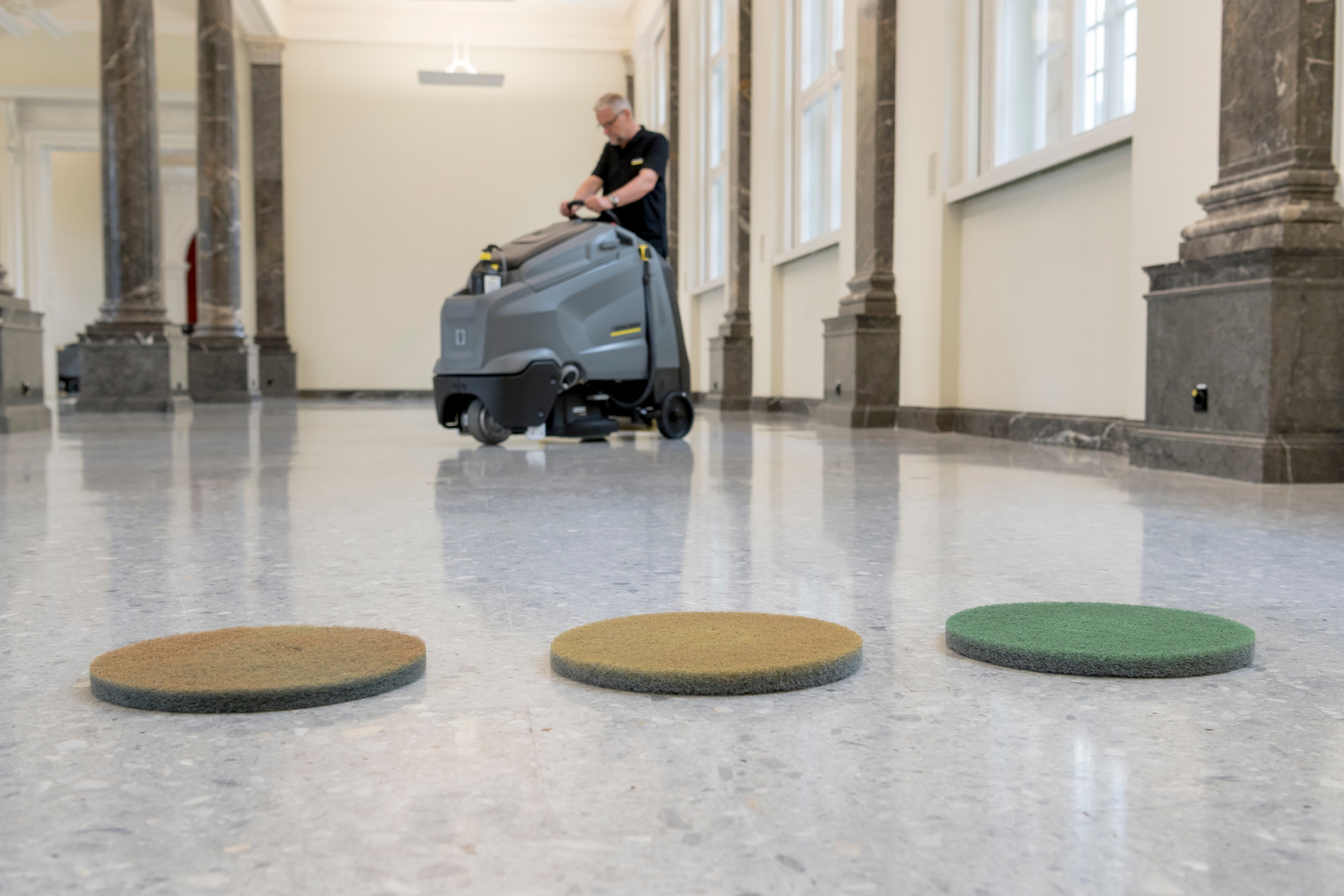
Renovation of lime-bound stones
When it comes to renovating lime-bound stones like marble, the method of polishing with diamond pads has prevailed in recent years. In order to achieve the original polished finish, a single-disc machine or scrubber drier with a disc scrubbing head should be guided over the floor covering between 10 and 15 times in two to three steps with diamond pads of different granulations (coarse, medium, fine). No cleaning agent should be used in this process, just clean water. Between the steps, you should remove lime sludge from the pads by rinsing them thoroughly.
However, deep cleaning beforehand is recommended in order to safely remove dirt, bodies of protective coating, lime stains and cement film.
Reinvigorate old high gloss finishes with crystallisation
Over time, continual use of polished stone floor coverings like Carrara marble will leave scratches and score marks. The gloss finish will be affected and the floor covering will become unsightly and have a matt finish. At the same time, resoiling is made easier and therefore greater cleaning efforts are required. To combat this trend and to reinvigorate the original high gloss finish, stone crystallisation will be required. There are two methods of crystallisation to choose from, depending on the required level of surface shine.
The benefits of crystallisation
Crystallisation produces a glossy look, gives the impression of cleanliness and retains the character of the stone. The surface is also hardened and compacted in the micro range, which is associated with increased resistance. Moreover, the surface remains breathable such that residual moisture can escape.
This results in
- a high-quality surface finish which lasts for longer,
- reduced resoiling,
- considerably more efficient maintenance cleaning,
- a consistently high cleaning quality,
- greater cost-effectiveness in cleaning and maintenance.
Additional methods for producing shiny natural stone floors
Method 1: Producing a high gloss finish using single-disc machine technology and crystallising agent powder
For all high-gloss, calcareous floor coverings, it is recommended that you use high-gloss crystallising agent powder with a single-disc machine. This treatment method gives the floor covering a "watery sheen", while also increasing its abrasion resistance. The colours and grain are also brought to the fore. In addition, the fact that the floors have been treated makes maintenance cleaning easier. If the floors are correctly maintained, the high gloss finish will be retained over a long period of time.
Preparation:
The use of a slow-running single-disc machine (180 rpm) in this crystallisation process has proven effective. You will also require an additional weight, a pad drive board, crystallisation pad and spray bottle for wetting the crystallising agent powder.
Steps:
- Firstly, the floor covering must be thoroughly cleaned, i.e. the glossy layers, protective coating and dirt build-up must be removed. This is undertaken according to the method previously outlined. The cleaned floor is then neutralised with clean water and left to dry.
- High gloss crystallising agent powder is evenly sprinkled (30 g/m²) on the thoroughly cleaned and dry floor and a moderate amount of water is then added using a spray bottle.
- The mixture is worked in using the crystallisation pad (silver) until it reaches a creamy consistency.
- Use the pad to work the crystallisation mixture until the material is used up and an even gloss is produced.
- Then brush out the material residues – particularly from the joints – using the single-disc machine, scrubbing brush and plenty of water and suck up the dirt using a wet and dry vacuum cleaner. Use a large surface wiping machine for postwiping, if necessary.
The area performance for this method is between 10 m²/h and 15 m²/h.
Method 2: Matt gloss thanks to wax-free, genuine stone fluorosilicate with roller technology
This alternative crystallisation method is suitable wherever a matt gloss finish will suffice and higher area performances are required. The floor covering intended for crystallisation must not be coated or pre-treated. However, if that were the case, it would first be necessary to perform deep cleaning or remove the coating.
Steps:
- Cover permanently installed objects to protect them from dust formation.
- If necessary, perform deep cleaning on the floor covering using the two-step method.
- Use a pump spray bottle to spray a liquid crystallising agent onto sections (10 ml/m²) of the dry floor covering.
- Use a waxer or large surface wiping machine to evenly spread the crystallising agent.
- Use the scrubber drier with green grit brushes to immediately apply the crystallising agent to the area.
- Slowly clean the area at full contact pressure multiple times until a gloss finish is produced.
- Use (soft) white brushes to rinse the area with clean water in order to pick up any dust produced during crystallisation.
The area performance for this process is between 100 m²/h and 350 m²/h, depending on the scrubber drier's working width, making this crystallisation method very efficient and cost-effective.
This method is also particularly well-suited to textured, hewn and calcareous natural stone floor coverings because the roller brushes themselves penetrate into the grooves and bring about the crystallisation effect.